People stories
Next-generation power systems
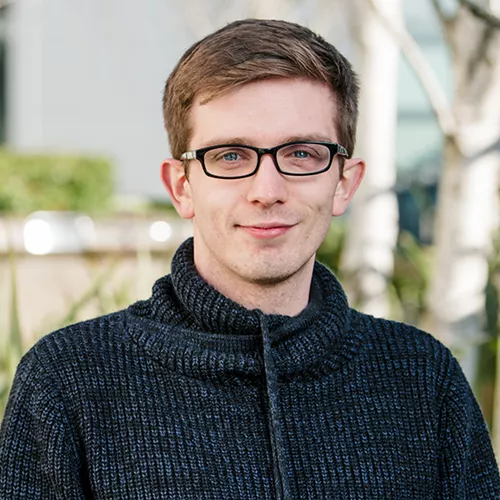
Harry
Research Manager - Design, UK
From summer intern to a lead in research engineering.
Motors, batteries and power systems are fascinating. They present a unique set of engineering challenges, bringing together areas of mechanical, thermal, electromagnetic and aero-acoustic design. As a multidisciplinary team at Dyson, we perform our own research as well as looking at cutting-edge technology from universities, aerospace companies and even NASA. Often, we start our projects from a blank sheet of paper; I really enjoy this creative, problem-solving side of my job.
Back in 2014, I began as a summer intern at Dyson, working on a project with the Motors and Power Systems Development team. I presented to some of the board, which was a great experience – I was excited, but a bit nervous, particularly given there was the possibility of a permanent job at the end of it. It showed that Dyson cared about getting its interns programme up and running, and were serious about involving us in projects. During that time, I got an insight into the interesting areas of technology being developed and the general direction of the company.
Following my internship, I was offered a graduate role, starting in September 2015. After a year as a graduate in development, I had the opportunity to do a secondment in research. I found this to be my true calling, so I decided to stay working in this area. It’s great that Dyson gives you the opportunity to discover what you truly want to do.
My current role is Lead Research Engineer working in the Technical Research team. We supply a lot of the motors and power electronics systems that go into Dyson machines, as well as feeding into energy storage research and next-generation technologies. We collaborate with the NPI teams to drive technological progress across the Dyson product range, as well as helping to create whole new categories. In some cases, we’re looking at things where there’s no precedent on the market and are truly exploring the unknown.
I’ve learnt a broad set of skills by interacting with all the different teams, bringing them together is a big challenge – the best engineering solution is always a careful, integrated design considering elements from many areas. I’ve also been able to develop my interpersonal skills by interacting with suppliers and presenting to senior executives who are always very interested in the projects we work on.
Since joining Dyson, I’ve been able to apply on a daily basis what I learnt during my degree in Mechanical Engineering. We deal with high-precision and complex systems, often using simulation tools to predict and model how things will behave in real life. I’ve learnt more about manufacturing processes through interacting with suppliers around the world, and now have a detailed appreciation of the things that need to happen in a successful supply chain. It’s amazing going from sketches in a book to a production line in Singapore and being able to produce a motor every few seconds.
Dyson is good at recruiting really interesting people. If you want to interact, people are very happy to share and help out. As an intern I thought I’d sit in the background, but there are loads of opportunities to learn and help others in turn. I really enjoy seeing the new generations of interns and graduates starting now and be able to work alongside them at the start of their careers.